Getting quality polished concrete results requires experience. There are multiple variables in the polishing process outside a contractor’s control that must be dealt with for successful projects.
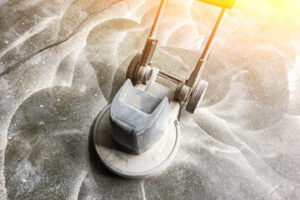
One common problem I see in the industry is contractors skipping grits in the processing sequence. This can lead to floors that lack overhead reflective clarity. Contact Concrete Polishing Contractor Waco TX for professional help.
Concrete polishing contractors offer cleaning services for commercial and industrial flooring. They provide air, tumble and wheel blasting as well as surface abrasion, paint and rust removal and concrete floor restoration and polishing. They also do epoxy and urethane coatings, line marking and surface preparation for commercial, food, retail, warehouse, hospital and showroom floors.
Cleaner floors create a safer environment for employees and customers. Dirty and dusty floors are not only unattractive, but they can also lead to higher instances of injury and health issues. With the right daily maintenance routine and regular polishing, polished concrete floors will maintain their beauty and safety for years to come.
A polished concrete floor can be stained and dyed to make it look like a variety of different flooring types such as marble or stone. This is done by acid washing the concrete then coloring it with either water based or solvent based dye. The color is then sealed to protect the flooring. This process is very eco-friendly and works well in hotels, hospitals, retail stores and high rise buildings.
Polished concrete is also denser than conventional flooring materials which can help prevent the penetration of liquids into sub-flooring. This can save on costly repairs and replacements. It is also easier to remove spills on a concrete floor with a polished finish. This is because the smooth surface does not allow the spill to settle and form stains. It is important to use neutral-ph cleaners on a polished concrete floor, since acidic chemicals can damage the surface. This is particularly important for high traffic areas. A concrete contractor can advise you on the best type of cleaner for your floor.
Preparation
The first step of concrete polishing involves cleaning the surface to remove any existing coatings, adhesives or contaminants. This is an important step because it ensures a clean and uniform substrate for the grinding and polishing process. It may take a day or two to complete this stage.
Next, the concrete is mechanically ground using progressively finer diamond-impregnated pads to smooth and refine the surface. This step can take several days depending on the size of the floor and the desired level of gloss. A penetrating chemical, called a densifier is sometimes used during this stage to increase the hardness of the concrete and make it more resistant to abrasion.
Once the concrete is ground and polished, control joints and cracks are filled with an appropriate filler material to achieve a consistent appearance. This prevents the concrete from becoming dull or scratched as it is moved around the facility and also eliminates the need for future repairs.
Lastly, a protective sealer is applied to the concrete to protect it from damage and keep it looking glossy. Reapplying a sealer every two to five years will keep the concrete beautiful and long-lasting.
By choosing a Concrete Polishing Contractor, your facility can benefit from an elegant, shiny, and durable floor that will enhance your company’s image and improve employee morale. Regular maintenance with sweeping, damp mopping, and the occasional high-speed burnish with an 1,800-grit pad will maintain the shine. And, since polished concrete is a structural component of your building, it won’t require replacement like other flooring options. That means a substantial savings for your business.
Grinding
Concrete polishing is a process of progressive grinding, honing, densification and polishing that turns a dull and unattractive concrete surface into an aesthetically pleasing, highly durable, dustproof, light reflective and functional floor system. It has become one of the most popular floor systems in commercial flooring and is used in new construction, warehouses, distribution centers and manufacturing facilities as well as hospitals, retail stores, and restaurants.
The contractor grinds the concrete with diamond-segmented abrasives that create a smooth and shiny surface. This is done either dry or wet, depending on the conditions and sheen specification. Initially coarse-grit abrasives are used, similar to sanding wood. As the concrete becomes smoother, a finer-grit abrasive is introduced that eventually achieves a glossy finish.
After the sheen is achieved, chemical products are applied that harden and seal the concrete surface. This protects the concrete from the abrasive effects of normal use and cleaning chemicals, reducing maintenance costs and downtime in busy operations. It also helps the floors resist abrasion from heavy machinery, which extends their useful working life.
The contractor then adds a stain-guard to the polished concrete to make it resistant to chemical stains such as juice, soda, bleach and battery acid that can discolor the concrete. This product seeps into the pores of the concrete, protecting it from abrasion and making it easier to clean.
To increase traction on the floor, the contractor may add an anti-slip grit additive to the final coat of sealer. This provides increased traction and prevents slipping, even when the floor is wet. The contractor may also recommend the addition of rubber mats or area rugs in high-traffic areas where traction is an issue.
Polishing
Concrete floor polishing involves specialized equipment that grinds the concrete’s surface with diamond disks to achieve the desired level of shine or smoothness. It’s not a do-it-yourself project, and it should only be undertaken by an experienced concrete polishing contractor. It’s a process that requires extensive knowledge of the equipment and the ability to follow all proper safety procedures.
There are both wet and dry methods of concrete polishing. A wet method uses water to cool the abrasive discs and help create a slurry to remove any dust. A dry method utilizes industrial vacuums to eliminate the need for water and produces a cleaner result.
The duration of the concrete polishing process depends on the desired sheen or gloss level and the size of the project area. A basic finish can be completed in one to two days for most industrial and commercial spaces. A high-end finish takes longer to complete and may require additional steps for more intricate design patterns and color matching.
During the grinding and polishing processes, your concrete contractors will also apply stain guards and anti-slip grit additives to enhance the look of the floor. These products are then sealed to provide a protective layer that resists oil, grease, and other chemicals.
Chemical resistance is a concern for many customers, especially in pharmaceutical or food processing facilities. While polished concrete is relatively resistant to etching and staining from most household and industrial cleaning products, strong acids and caustic chemicals will discolor and damage any unprotected concrete.
For this reason, your concrete flooring contractors will most likely recommend a chemical-resistant performance coating. It’s an easy way to add a beautiful, long-lasting appearance while protecting your concrete floors from the damage that chemicals can cause.
Sealing
Concrete is very porous & absorbs a lot of water, chemicals & oil. This can cause the concrete to deteriorate, leading to cracks & spalling. To avoid this, a protective sealer is often applied to the surface. A professional contractor can recommend the best sealer for your space & situation. Depending on your facility, you might choose a penetrating concrete densifier, a siloxane sealer, an acrylic sealer or a polyurethane sealer.
When the surface is dry, it can be burnished to achieve a high-gloss sheen. The process involves using a machine that heats, melts & buffs the sealant into a polished concrete surface. This will prevent dusting & protect the floor from stains & moisture.
The specialized equipment used to grind & polish concrete floors can be expensive, heavy & difficult to operate if you don’t know what you’re doing. Trying to perform these tasks on your own could result in expensive damage to the concrete, personal injury & a big mess to clean up.
A professional masonry contractor will have the proper equipment to do the job in a timely manner & within budget. It’s important to prepare the area before their arrival & have any inventory, stock or furniture moved out of the way so it doesn’t get damaged. It’s also a good idea to close off any areas that can be affected by dust or water.
It’s also a good idea to wear a respirator approved for working with volatile organic compounds (VOCs) as they are present in some of the coatings & sealers used on warehouse concrete. VOCs are known to cause short & long term health effects. A properly sealed concrete floor will last much longer than unprotected concrete & is less expensive to maintain.